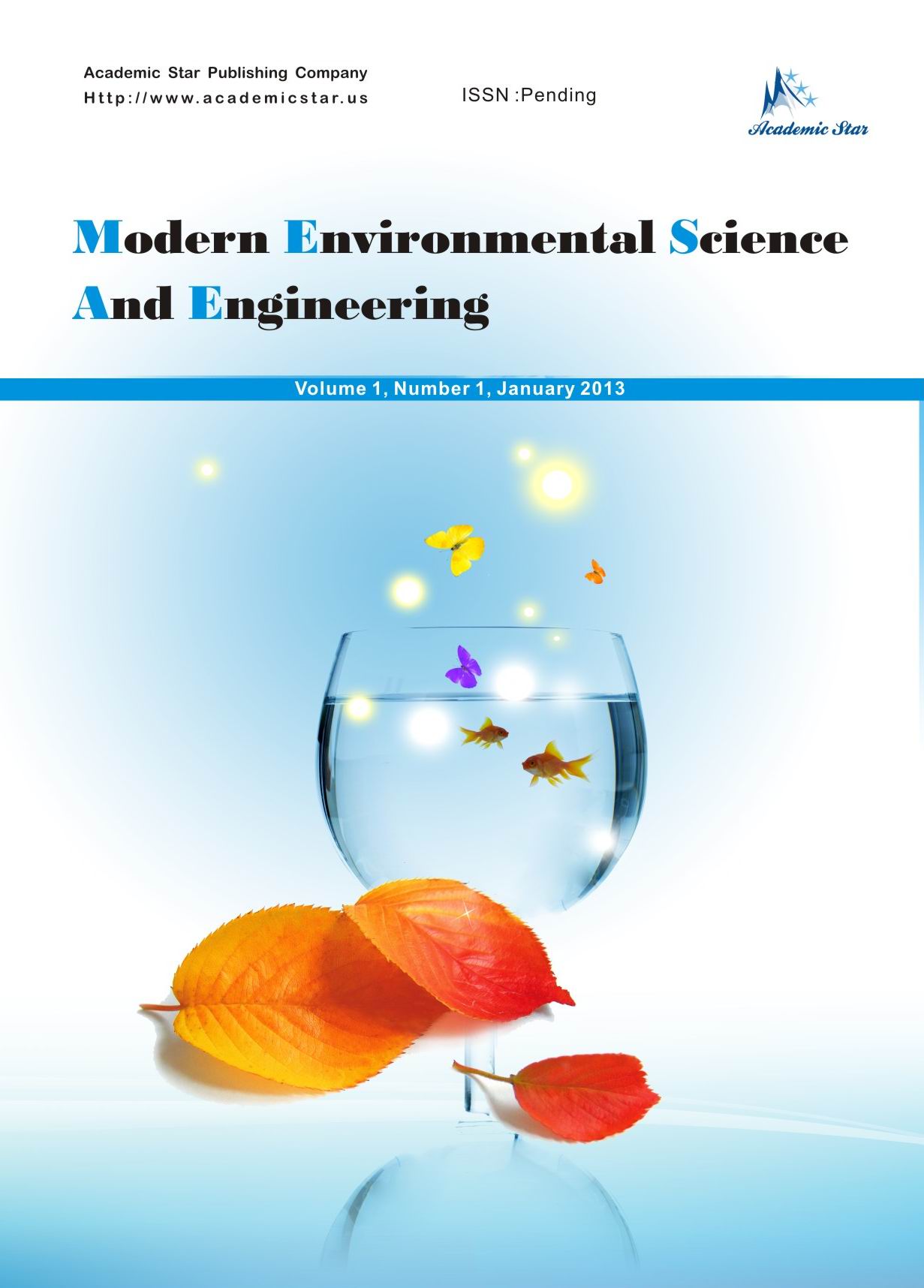
- ISSN: 2333-2581
- Modern Environmental Science and Engineering
Caterpillar — A Gcode Translator in Grasshopper
Hao Zheng1, Barrak Darweesh2, Heewon Lee3, and Li Yang4
4. University of Sydney, Sydney, Australia
Abstract: Additive manufacturing has widely been spread in the digital fabrication and design fields, allowing designers to rapidly manufacture complex geometry. In the additive process of Fused Deposition Modelling (FDM), machine movements are provided in the form of Gcode - A language of spatial coordinates controlling the position of the 3D printing extruder. Slicing software use closed mesh models to create Gcode from planar contours of the imported mesh, which raises limitations in the geometry types accepted by slicing software as well as machine control freedom. This paper presents a framework that makes full use of three degrees of freedom of Computer Numerically Controlled (CNC) machines through the generation of Gcode in the Rhino and Grasshopper environment. Eliminating the need for slicing software, Gcode files are generated through user-defined toolpaths that allow for higher levels of control over the CNC machine and a wider range of possibilities for non-conventional 3D printing applications. Here, we present Caterpillar, a Grasshopper plug-in providing architects and designers with high degrees of customizability for additive manufacturing. Core codes are revealed, application examples of printing with user-defined toolpaths are shown.